Green Initiatives
Sky Bracket is dedicated to providing both safe and effective products to its customers through the most eco-friendly methods available.
Water based bio degradable and earth friendly coolant is used for all in house machining operations. All coolant used by Sky Bracket is cleaned and checked for metal particles then recycled. Additionally, synthetic oil is used by all of our CNC machines, which lasts longer than traditional oil and is more easily recycled.
All castings sold by Sky Bracket were manufactured by Olson Aluminum Castings. By selling products created by a “green foundry,” we can be sure that our products are created and packaged in the most efficient and eco-friendly methods currently available. Because the foundry that produces our castings is located a mere 100 feet from the Sky Bracket warehouse, the castings are able to be transferred from the foundry to the Sky Bracket assembly facility without the use of packing materials or shipping emissions.
Listed below are several steps the foundry that produces Sky Bracket’s castings have taken to become a “green foundry.”
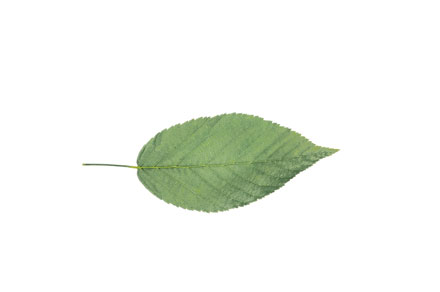
Green Sand
Our “petro-bond” green sand system and molding process is a continuous recycling act. Following shakeout, the used sand is sent back to the sand muller and with minimal additives, it is ready again to produce additional molds. Of the approximate 100 tons of sand continually used on a daily basis, only a mere 200 lbs of new silica sand is required to be added to the system.
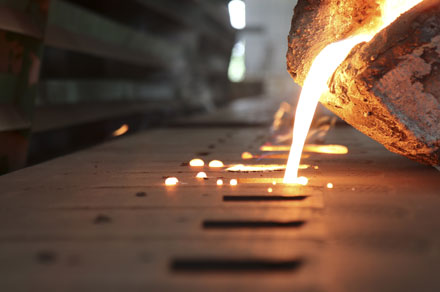
Core Sand
Currently all of our used core sand is transported from our facility to be used as landfill cover and road bed aggregate. Additionally, we are in the process of implementing a no-bake core mold line with an ALpHASET® binder system. This resin binder is water based, rather than petrochemical solvents, which will dramatically reduce the amount of VOC and HAP emissions.
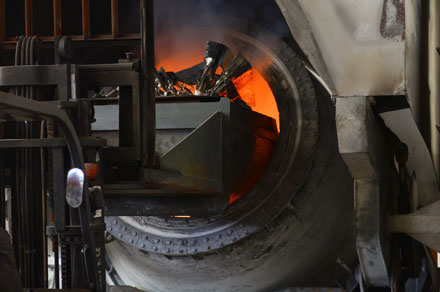
Aluminum
All of the aluminum that we process and pour, is shipped as a finished product or is re-melted to be utilized for subsequent castings. Our aluminum alloys typically consist of 50% in-house return metal which includes all gates, risers, runner bars and floor returns along with the balance consisting of newly alloyed ingot. This controlled alloying process eliminates virtually all waste or aluminum alloy from reaching the landfill.

Lighting
The latest reduction in energy consumption came when Olson Aluminum Castings replaced the lighting system from high pressure sodium bulbs to energy efficient metal halide providing brighter, whiter light with less wattage. The foundry will save 56,284 kWh annually, which equals enough energy to heat 5 homes per year and take 4 cars off the road per year.
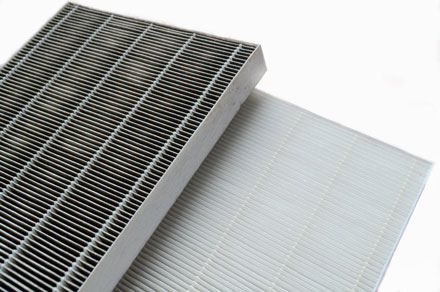
Air Filtration
Our internal air filtration system and dust collection units continually filter the foundry environment of “dirty” airborne particulates and returns clean air to the facility during all hours of production.
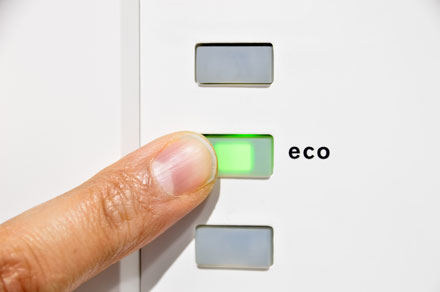
Conserving Heat (Energy)
The foundry uses virtually no dedicated heating system. Heat generated during the melting process is utilized to heat the rest of the foundry during cooler months. Radiant heat from an adjacent heat treat furnace is used to keep the hot water quench tank in our heat treat process at an operating temperature of 170° F. Moreover, energy consuming operations such as furnaces, are controlled by programmed timers thereby limiting unnecessary, and wasteful demand on both natural gas and electricity